Monitoring and control of cyber-physical systems.
Event
HumanSys 2017
1st International Workshop on Human-centered Sensing, Networking, and Systems (HumanSys 2017)
Co-located with ACM SenSys 2017
Equipment operation represents one of the most dangerous tasks on a construction sites and accidents related to such operation often result in death and property damage on the construction site and the surrounding area. Such accidents can also cause considerable delays and disruption, and negatively impact the efficiency of operations. This award will conduct research to improve the safety and efficiency of cranes by integrating advances in robotics, computer vision, and construction management. It will create tools for quick and easy planning of crane operations and incorporate them into a safe and efficient system that can monitor a crane's environment and provide control feedback to the crane and the operator. Resulting gains in safety and efficiency will reduce fatal and non-fatal crane accidents. Partnerships with industry will also ensure that these advances have a positive impact on construction practice, and can be extended broadly to smart infrastructure, intelligent manufacturing, surveillance, traffic monitoring, and other application areas. The research will involve undergraduates and includes outreach to K-12 students. The work is driven by the hypothesis that the monitoring and control of cranes can be performed autonomously using robotics and computer vision algorithms, and that detailed and continuous monitoring and control feedback can lead to improved planning and simulation of equipment operations. It will particularly focus on developing methods for (a) planning construction operations while accounting for safety hazards through simulation; (b) estimating and providing analytics on the state of the equipment; (c) monitoring equipment surrounding the crane operating environment, including detection of safety hazards, and proximity analysis to dynamic resources including materials, equipment, and workers; (d) controlling crane stability in real-time; and (e) providing feedback to the user and equipment operators in a "transparent cockpit" using visual and haptic cues. It will address the underlying research challenges by improving the efficiency and reliability of planning through failure effects analysis and creating methods for contact state estimation and equilibrium analysis; improving monitoring through model-driven and real-time 3D reconstruction techniques, context-driven object recognition, and forecasting motion trajectories of objects; enhancing reliability of control through dynamic crane models, measures of instability, and algorithms for finding optimal controls; and, finally, improving efficiency of feedback loops through methods for providing visual and haptic cues.
Off
University of Illinois at Urbana-Champaign
-
National Science Foundation

Computer systems are increasingly coming to be relied upon to augment or replace human operators in controlling mechanical devices in contexts such as transportation systems, chemical plants, and medical devices, where safety and correctness are critical. A central problem is how to verify that such partially automated or fully autonomous cyber-physical systems (CPS) are worthy of our trust. One promising approach involves synthesis of the computer implementation codes from formal specifications, by software tools. This project contributes to this "correct-by-construction" approach, by developing scalable, automated methods for the synthesis of control protocols with provable correctness guarantees, based on insights from models of human behavior. It targets: (i) the gap between the capabilities of today's hardly autonomous, unmanned systems and the levels of capability at which they can make an impact on our use of monetary, labor, and time resources; and (ii) the lack of computational, automated, scalable tools suitable for the specification, synthesis and verification of such autonomous systems. The research is based on study of modular reinforcement learning-based models of human behavior derived through experiments designed to elicit information on how humans control complex interactive systems in dynamic environments, including automobile driving. Architectural insights and stochastic models from this study are incorporated with a specification language based on linear temporal logic, to guide the synthesis of adaptive autonomous controllers. Motion planning and other dynamic decision-making are by algorithms based on computational engines that represent the underlying physics, with provision for run-time adaptation to account for changing operational and environmental conditions. Tools implementing this methodology are validated through experimentation in a virtual testing facility in the context of autonomous driving in urban environments and multi-vehicle autonomous navigation of micro-air vehicles in dynamic environments. Education and outreach activities include involvement of undergraduate and graduate students in the research, integration of the research into courses, demonstrations for K-12 students, and recruitment of research participants from under-represented demographic groups. Data, code, and teaching materials developed by the project are disseminated publicly on the Web.
Off
University of Washington
-
National Science Foundation
By 2050, 70% of the world's population is projected to live and work in cities, with buildings as major constituents. Buildings' energy consumption contributes to more than 70% of electricity use, with people spending more than 90% of their time in buildings. Future cities with innovative, optimized building designs and operations have the potential to play a pivotal role in reducing energy consumption, curbing greenhouse gas emissions, and maintaining stable electric-grid operations. Buildings are physically connected to the electric power grid, thus it would be beneficial to understand the coupling of decisions and operations of the two. However, at a community level, there is no holistic framework that buildings and power grids can simultaneously utilize to optimize their performance. The challenge related to establishing such a framework is that building control systems are neither connected to, nor integrated with the power grid, and consequently a unified, global optimal energy control strategy at a smart community level cannot be achieved. Hence, the fundamental knowledge gaps are (a) the lack of a holistic, multi-time scale mathematical framework that couples the decisions of buildings stakeholders and grid stakeholders, and (b) the lack of a computationally-tractable solution methodology amenable to implementation on a large number of connected power grid-nodes and buildings.
In this project, a novel mathematical framework that fills the aforementioned knowledge gaps will be investigated, and the following hypothesis will be tested: Connected buildings, people, and grids will achieve significant energy savings and stable operation within a smart city. The envisioned smart city framework will furnish individual buildings and power grid devices with custom demand response signals. The hypothesis will be tested against classical demand response (DR) strategies where (i) the integration of building and power-grid dynamics is lacking and (ii) the DR schemes that buildings implement are independent and individual. By engaging in efficient, decentralized community-scale optimization, energy savings will be demonstrated for participating buildings and enhanced stable operation for the grid are projected, hence empowering smart energy communities. To ensure the potential for broad adoption of the proposed framework, this project will be regularly informed with inputs and feedback from Southern California Edison (SCE). In order to test the hypothesis, the following research products will be developed: (1) An innovative method to model a cluster of buildings--with people's behavior embedded in the cluster's dynamics--and their controls so that they can be integrated with grid operation and services; (2) a novel optimization framework to solve complex control problems for large-scale coupled systems; and (3) a methodology to assess the impacts of connected buildings in terms of (a) the grid's operational stability and safety and (b) buildings' optimized energy consumption. To test the proposed framework, a large-scale simulation of a distribution primary feeder with over 1000 buildings will be conducted within SCE?s Johanna and Santiago substations in Central Orange County.
Off
University of California-Riverside
-
National Science Foundation
Nanpeng Yu
Project
CPS: Synergy: Collaborative Research: Real-time Data Analytics for Energy Cyber-Physical Systems
Inadequate system understanding and inadequate situational awareness have caused large-scale power outages in the past. With the increased reliance on variable energy supply sources, system understanding and situational awareness of a complex energy system become more challenging. This project leverages the power of big data analytics to directly improve system understanding and situational awareness. The research provides the methodology for detecting anomalous events in real-time, and therefore allow control centers to take appropriate control actions before minor events develop into major blackouts. The significance for the society and for the power industry is profound. Energy providers will be able to prevent large-scale power outages and reduce revenue losses, and customers will benefit from reliable energy delivery with service guarantees. Students, including women and underrepresented groups, will be trained for the future workforce in this area.
The project includes four major thrusts: 1) real-time anomaly detection from measurement data; 2) real-time event diagnosis and interpretation of changes in the state of the network; 3) real-time optimal control of the power grid; 4) scientific foundations underpinning cyber-physical systems. The major outcome of this project is practical solutions to event or fault detection and diagnosis in the power grid, as well as prediction and prevention of large-scale power outages.
Off
New Jersey Institute of Technology
-
National Science Foundation
Due to their increasing use by civil and federal authorities and vast commercial and amateur applications, Unmanned Aerial Systems (UAS) will be introduced into the National Air Space (NAS); the question is only how this can be done safely. Today, NASA and the FAA are designing a new, (NextGen) automated air traffic control system for all aircraft, manned or unmanned. New algorithms and tools will need to be developed to enable computation of the complex questions inherent in designing such a system while proving adherence to rigorous safety standards. Researchers must develop the tools of formal analysis to be able to address the UAS in the NAS problem, reason about UAS integration during the design phase of NextGen, and tie this design to on-board capabilities to provide runtime System Health Management (SHM), ensuring the safety of people and property on the ground. This proposal takes a holistic view and integrates advances in the state of the art from three intertwined perspectives to address safe integration of unmanned systems into the national airspace: from on-board the vehicle, from the environment (NAS), and from the underlying theory enabling their formal analysis. There has been rapid development of new UAS technologies yet few of them are formally mathematically rigorous to the degree needed for FAA safety-critical system certification. This project bridges that gap, integrating new UAS and air traffic control designs with advances in formal analysis. Within the wealth of promising directions for autonomous UAS capabilities, this project fills a unique need, providing a direct synergy between on-board UAS SHM, the NAS environment in which they must operate, and the theoretical foundations common to both of these.
This research will help to build a safer NAS with increased capacity for UAS and create broadly impactful capabilities for SHM on-board UAS. Advancements will require theoretical research into more scalable model checking and debugging of safety properties. Safety properties express the sentiment that "something bad does not happen" during any system execution; they represent the vast majority of the requirements for NextGen designs and all requirements researchers can monitor on-board a UAS for system heath management during runtime. This research will tackle new frontiers in embedding health management capabilities on-board UAS. Collaborations with aerospace system designers at the National Aeronautics and Space Administration and tool designers at the Bruno Kessler Foundation will aid real-life utility and technology transfer. Broader impact will be achieved by involving undergraduate students in the design of an open-source, affordable, all-COTS and 3D-printable UAS, which will facilitate flight testing of this project's research advances. An open-UAS design for academia will be useful both for classroom demonstrations and as a research platform. Further impact will be achieved by using this UAS and the research it enables in interactive teaching experiences for K-12, undergraduate, and graduate students and in mentoring outreach specifically targeted at girls achieving in Science, Technology, Engineering and Mathematics (STEM) subjects.
Off
University of Cincinnati
-
National Science Foundation
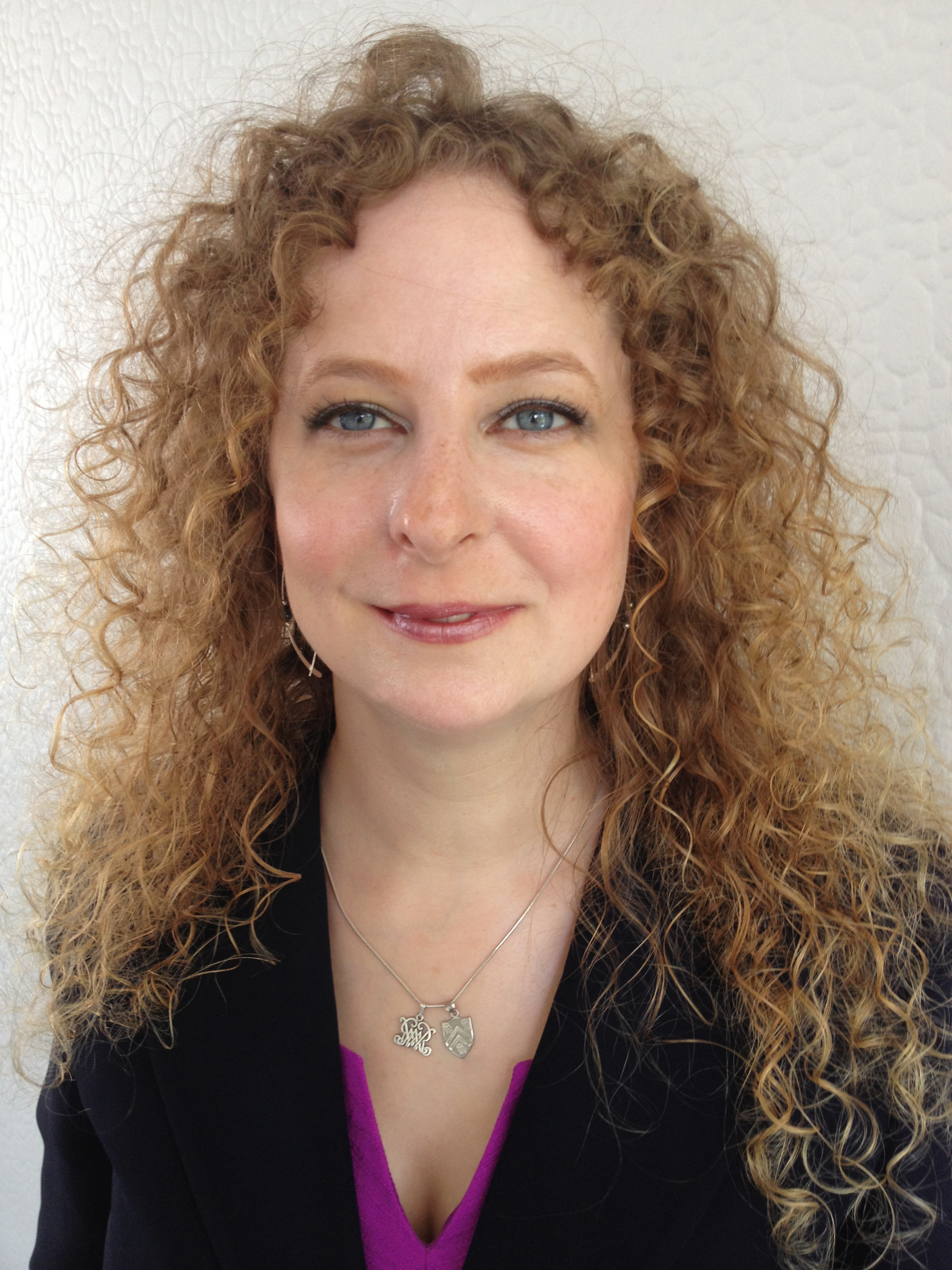
Software-Defined Control (SDC) is a revolutionary methodology for controlling manufacturing systems that uses a global view of the entire manufacturing system, including all of the physical components (machines, robots, and parts to be processed) as well as the cyber components (logic controllers, RFID readers, and networks). As manufacturing systems become more complex and more connected, they become more susceptible to small faults that could cascade into major failures or even cyber-attacks that enter the plant, such as, through the internet. In this project, models of both the cyber and physical components will be used to predict the expected behavior of the manufacturing system. Since the components of the manufacturing system are tightly coupled in both time and space, such a temporal-physical coupling, together with high-fidelity models of the system, allows any fault or attack that changes the behavior of the system to be detected and classified. Once detected and identified, the system will compute new routes for the physical parts through the plant, thus avoiding the affected locations. These new routes will be directly downloaded to the low-level controllers that communicate with the machines and robots, and will keep production operating (albeit at a reduced level), even in the face of an otherwise catastrophic fault. These algorithms will be inspired by the successful approach of Software-Defined Networking. Anomaly detection methods will be developed that can ascertain the difference between the expected (modeled) behavior of the system and the observed behavior (from sensors). Anomalies will be detected both at short time-scales, using high-fidelity models, and longer time-scales, using machine learning and statistical-based methods. The detection and classification of anomalies, whether they be random faults or cyber-attacks, will represent a significant contribution, and enable the re-programming of the control systems (through re-routing the parts) to continue production.
The manufacturing industry represents a significant fraction of the US GDP, and each manufacturing plant represents a large capital investment. The ability to keep these plants running in the face of inevitable faults and even malicious attacks can improve productivity -- keeping costs low for both manufacturers and consumers. Importantly, these same algorithms can be used to redefine the production routes (and machine programs) when a new part is introduced, or the desired production volume is changed, to maximize profitability for the manufacturing operation .
Off
Cornell University
-
National Science Foundation

Software-Defined Control (SDC) is a revolutionary methodology for controlling manufacturing systems that uses a global view of the entire manufacturing system, including all of the physical components (machines, robots, and parts to be processed) as well as the cyber components (logic controllers, RFID readers, and networks). As manufacturing systems become more complex and more connected, they become more susceptible to small faults that could cascade into major failures or even cyber-attacks that enter the plant, such as, through the internet. In this project, models of both the cyber and physical components will be used to predict the expected behavior of the manufacturing system. Since the components of the manufacturing system are tightly coupled in both time and space, such a temporal-physical coupling, together with high-fidelity models of the system, allows any fault or attack that changes the behavior of the system to be detected and classified. Once detected and identified, the system will compute new routes for the physical parts through the plant, thus avoiding the affected locations. These new routes will be directly downloaded to the low-level controllers that communicate with the machines and robots, and will keep production operating (albeit at a reduced level), even in the face of an otherwise catastrophic fault. These algorithms will be inspired by the successful approach of Software-Defined Networking. Anomaly detection methods will be developed that can ascertain the difference between the expected (modeled) behavior of the system and the observed behavior (from sensors). Anomalies will be detected both at short time-scales, using high-fidelity models, and longer time-scales, using machine learning and statistical-based methods. The detection and classification of anomalies, whether they be random faults or cyber-attacks, will represent a significant contribution, and enable the re-programming of the control systems (through re-routing the parts) to continue production.
The manufacturing industry represents a significant fraction of the US GDP, and each manufacturing plant represents a large capital investment. The ability to keep these plants running in the face of inevitable faults and even malicious attacks can improve productivity -- keeping costs low for both manufacturers and consumers. Importantly, these same algorithms can be used to redefine the production routes (and machine programs) when a new part is introduced, or the desired production volume is changed, to maximize profitability for the manufacturing operation .
Off
University of Michigan Ann Arbor
-
National Science Foundation
Kira Barton
James Moyne
Event
DHS 2017
International Workshop on Methods and Tools for Distributed Hybrid Systems (DHA 2017)
Associated with MFCS 2017
Event
WATERS 2017
8th International Workshop on Analysis Tools and Methodologies for Embedded and Real-time Systems (WATERS 2017)
June 27th, 2017 | Dubrovnik, Croatia | http://waters2017.inria.fr